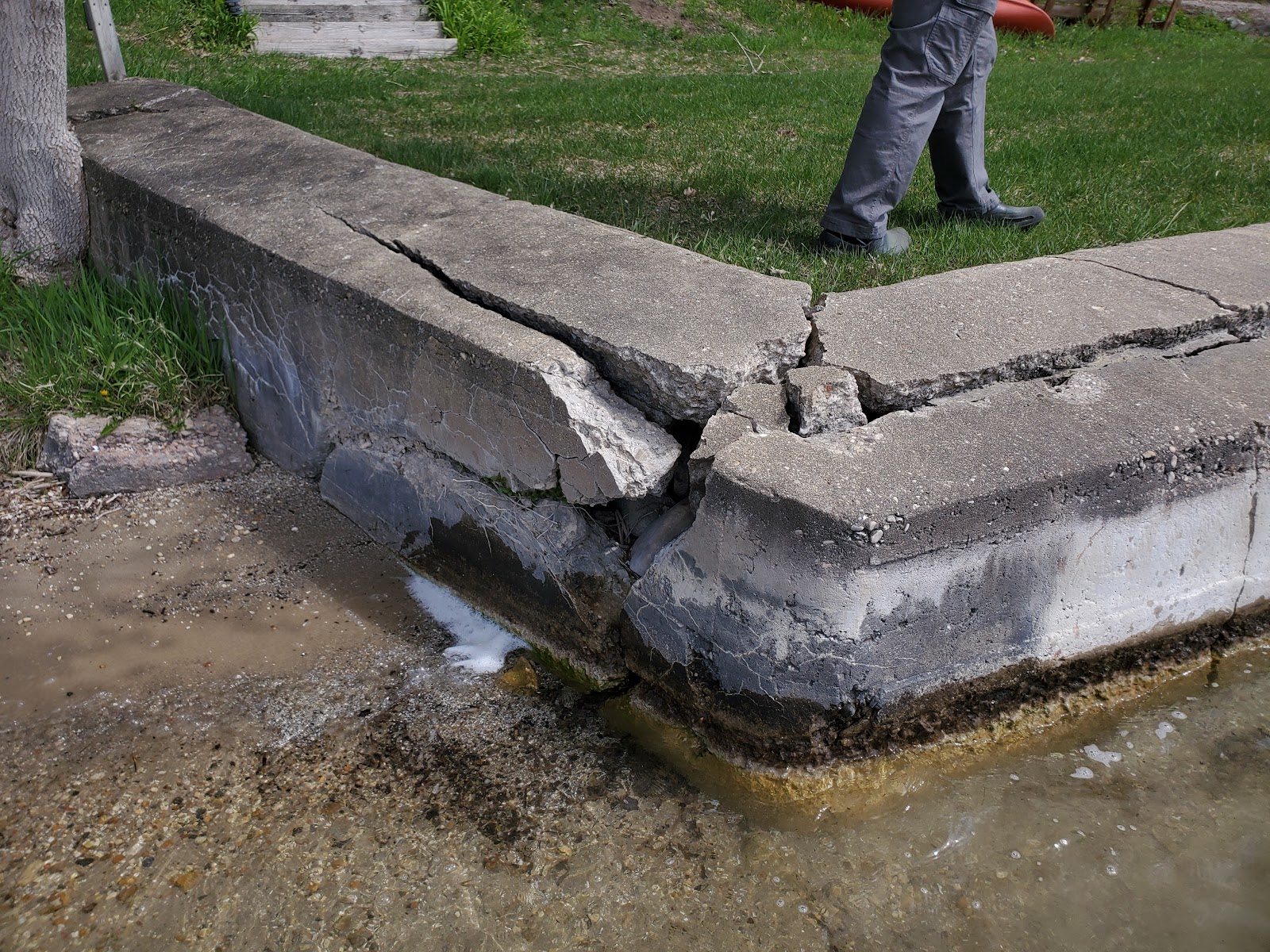
Case Study – Restoration of Crumbling 1950’s Concrete Seawall
This is a case study on cost effective restoration of very deteriorated 1950’s concrete seawall in south east Wisconsin where the breakwall was nearly beyond repair.
Two owners on an Oconomowoc area lake share 120 feet of a concrete breakwall that was failing quickly. The cracks, spalling and even exposed metal rebar were starting to accelerate each season and they needed to do something before the wall was past the point of no repair. They liked the legally grandfathered concrete breakwall and did not want the high cost or removal of the concrete wall and replacement with the only other option available to them, a natural stone grade to waterline. They were looking for a more cost effective solution and to keep the existing breakwall in place.
The Problem:
The wall was likely built in the 1950’s. It was a construction style common in SE Wisconsin where there was a 10-16” vertical poured concrete wall with a separate 18-24” cap poured on top with a slope to the lake.
Upon inspection it could be seen that the cap was separating from the wall and destabilizing the structure. As was also common in those days for the builders to throw random pieces of metal into the concrete along with actual rebar to try to reinforce the structure. Unfortunately, this untethered random metal made things worse. As the metal corroded with age, it expanded and caused spalling and more cracks. There had also been some trees, now removed, that had put pressure on the wall to cause movement. The cracks, wave action and muskrat also utilized the wall penetrations to allow water to erode soil behind the wall and sink holes were prevalent along the property. The owners could not keep up with filling them as the problem continued to get worse. Each season of freeze/thaw cycling have been accelerating the decomposition of the structure. In our opinion the wall only had a couple seasons before it passed the point of repair.
The Solution:
A four step process was implemented in this case. First, a Coast Guard approved marine grade polymer grout was injected under high pressure 2-4’ deep into the soil in back of the wall to consolidate the eroded soil so no further erosion would occur behind the wall. The polymer grout chosen was hydrophilic so it followed the cracks in the concrete from behind the wall. This sealed and consolidated the decomposing concrete from behind and under the soil. The polymer grout also expanded into the many air voids that were found behind the wall. This was done with no excavation.
Second, the large cracks under the water line were sealed with a combination of marine grade expanding polymer grout soaked into high strength natural fiber ropes. When these polymer soaked ropes are pressed into the cracks they expand on contact with the water and fill the crack with a nearly indestructible rubbery seal that repels pests such as muskrat and is robust to freeze thaw cycling.
Third, the concrete spalls and cracks were patched and refilled. The loose debris was removed and the inside surface of the spalls were cleaned. The open spalled areas were drilled and coated metal fasteners were applied to provide additional mechanical bonding. An ultra high tensile fiber reinforced concrete product by BASF typically utilized for vertical bridge concrete repair was hand poured and trowled into the spalls and cracks.
Fourth: The problem of the water draining from the significant hill behind the breakwall had to be addressed. As with any shoreline rainwater needs to get to the lake and it will find the best path. Now that the wall was sealed and the soil is consolidated the water will back up behind the wall and cause softening of the soil and remain wet. The solution in this case was to bore 2.5” diameter drain holes into the face of the concrete breakwall approximately 2-3 feet deep and every 5 feet along the wall. Then a jet filter cap was applied over the hole. This allowed rainwater to flow in a controlled manner to the lake and the jet filter keeps debris from getting in and out and prevents pests from utilizing the core holes.
Outcome:
Before
After
The amount of patching concrete required to be hand carried down the hill was much higher than expected as the extent of the deteriorated concrete became apparent. The owners were happy with the appearance of the wall and the fact that no excavation was required. The job took 5 days to complete. The wall was not coated at the time of these photos, but the owners opted to have a BASF breathable cementitious coating applied to further improve the appearance and extend the lifespan. No permit was required for this job because no excavation was done and the shape, function and footprint of the wall was not changed. The work was completed with no environmental impact to the lake or owners lawn and landscaping. This solution will add 10-20 years of continued service to this seawall. For the economic assessment of the project it was determined that the final total project cost was approximately 1/3rd the cost of removal and replacement with natural stone gradient per Wisconsin DNR regulations.
If you want to learn more about options for shoreline restoration, maintenance or landscaping, please contact us for a free consultation.